Climbers and Canyon folk often worry about how hot a rap
device gets, and whether the device will burn through the rope when they
suddenly stop mid-rappel. Hence they worry about “heat dissipation.” Many think
aluminum devices should be much better at heat dissipation, because aluminum
has such a high thermal conductivity.
Actually, the high thermal conductivity is the reason
aluminum devices get so hot so quickly. Heat is generated in the rope in two
ways; 1) by the surface friction at the rope-metal contact; 2) and by “internal
friction” by bending and deforming the rope as it goes around the friction
device and carabiner. Each is roughly half the heat production in the rope. The heat
generated by surface friction gets divided between the rope and the metal
device; the faster the rope goes past the device, and the lower the thermal conductivity
of the metal device, the greater the fraction of the heat that goes into the
rope. This
“direct heating” of the rope
rarely increases the rope temperature by more than 10C, because the
total mass of rope is so great-- e.g. for a two-strand 30m rap, the rope heating
might be spread over 3000 grams. For the metal device,
conductive-convective
cooling by the air is more important than radiative cooling, and all
devices
face that limit, though it depends somewhat on the metal used to create them. If the
rate of
heat absorption in the metal device (heat generated by rope-device interaction) is too slow, it is eventually
balanced by the heat losses due to conduction-convection.
The above figure (at left) is mainly illustrative, calculated
from Eqn 6 in Berry and Barber (1984, Journal of Tribology vol 106, p 408), for
a heat source that “ploughs” into a softer, moving substance. As the speed of
the rope increases, the greater the fraction of the heat that gets distributed
in the rope; and for Titanium Grade 2 and 304 Stainless, a much greater
fraction goes into the rope, compared to 7075 aluminum (which is typically used
in carabiners and climbing devices).
In the middle (above) is an IR video of a rope going over a munter
on a carabiner made of 7075 aluminum. At right is a video of the same rope going
over a screwlink made of Grade 2 titanium; both Al and Ti devices
were ~9mm in diameter. The aluminum
heats up much more substantially than the titanium device. The ambient
was about 40F, as I had to do the test in pre-dawn darkness, backed up
by black plastic. The lower end of the
scale for titanium gives a false temperature, as explained below.
There are two artifacts; first is that the IR camera is
assuming everything has an emissivity of ~0.95, which is true for the fabric,
so the best temperature indications likely come from the center of the Munter.
The aluminum carabiner is heavily anodized, and likely has an emissivity of ~0.85.
However, the Ti is a wild card, as its emissivity may be from 0.4-0.8. (The Ti
is certainly oxidized, but the extent is unknown.) The Ti, which was at ~40F initially,
is emitting as if it were at a lower temperature than the black plastic that
forms the background. Second, the Ti carabiner is actually reflecting the IR
emitted by the hot spot, so the seemingly high readings off the edges are not
real. Nonetheless, I can vouch that the
Ti felt cool at the end of the test, whereas the Al felt quite warm.
Thus the temperature at the center of the Munter is the hot
spot, but is quite a bit colder in the Ti carabiner. Part of the rope heat is
from surface friction at the very contact with the biners, but ~half of the
rope heat is from internal friction—the bending and deformation as the rope
goes over the biners.
N.B.:
The rope was 6mm polyester-covered Dyneema, and force was
applied at ~70lbs, by attaching one end of the rope to a linescale 3 load cell,
which was then attached to my harness. I then walked backwards hard, using the
other line in my “brake hand” to keep the force reading ~70 lbs on the load
cell, over ~45’. Obviously a real rap could generate a lot more force and more heat, but I'm looking for relative changes only.
Postscript: Thermocouple Testing
I took the same Ti and Al devices, and
affixed calibrated meat thermometer thermocouples (TC) to them, as
shown in the picture below (click on the thumbnail to see the larger
image). The tips of the thin TCs are placed as shown; Al foil and
thermal grease (Arctic MX-6) were used to attempt a good thermal
coupling. The TC itself pertutbs the temperature. The mass of the Ti
device is 2x that of the Al device, but most of that mass is well above
the TC contact. The attempt here was to place the TCs at the same
distance from the munter position on the devices.
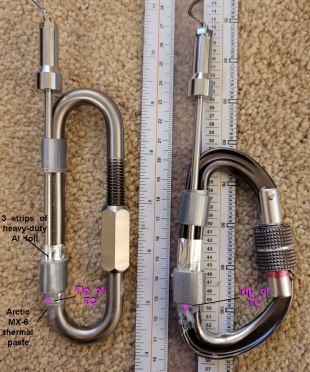
The exact same tests, as described above, were repeated, pulling a
munter in 6mm polyester-sheathed rope through the devices for ~45' at 70+/- 10
lbs force.
One test with the Al biner brought the TC temps up 50 degrees F; two
tests with the Ti device brought the the temperature up by 12F, and
then 11F. So as expected, the Al device sees a 4-5x temperature rise
under the same conditions.
|